Understanding Porosity in Welding: Checking Out Reasons, Effects, and Avoidance Techniques
As specialists in the welding sector are well aware, comprehending the reasons, effects, and avoidance techniques associated to porosity is critical for achieving robust and reliable welds. By diving into the root triggers of porosity, analyzing its destructive impacts on weld top quality, and discovering effective prevention techniques, welders can improve their expertise and skills to produce top quality welds constantly.
Usual Sources Of Porosity
Contamination, in the form of dust, oil, or corrosion on the welding surface area, develops gas pockets when heated up, leading to porosity in the weld. Inappropriate shielding takes place when the protecting gas, generally used in procedures like MIG and TIG welding, is incapable to fully shield the liquified weld swimming pool from responding with the bordering air, resulting in gas entrapment and succeeding porosity. Furthermore, insufficient gas insurance coverage, frequently due to inaccurate flow prices or nozzle positioning, can leave components of the weld unprotected, permitting porosity to create.
Effects on Weld High Quality
The presence of porosity in a weld can dramatically compromise the overall quality and honesty of the bonded joint. Porosity within a weld develops voids or tooth cavities that deteriorate the structure, making it a lot more vulnerable to fracturing, corrosion, and mechanical failing.
In addition, porosity can impede the efficiency of non-destructive testing (NDT) methods, making it challenging to find other defects or suspensions within the weld. This can result in significant safety and security problems, particularly in vital applications where the structural integrity of the welded elements is extremely important.
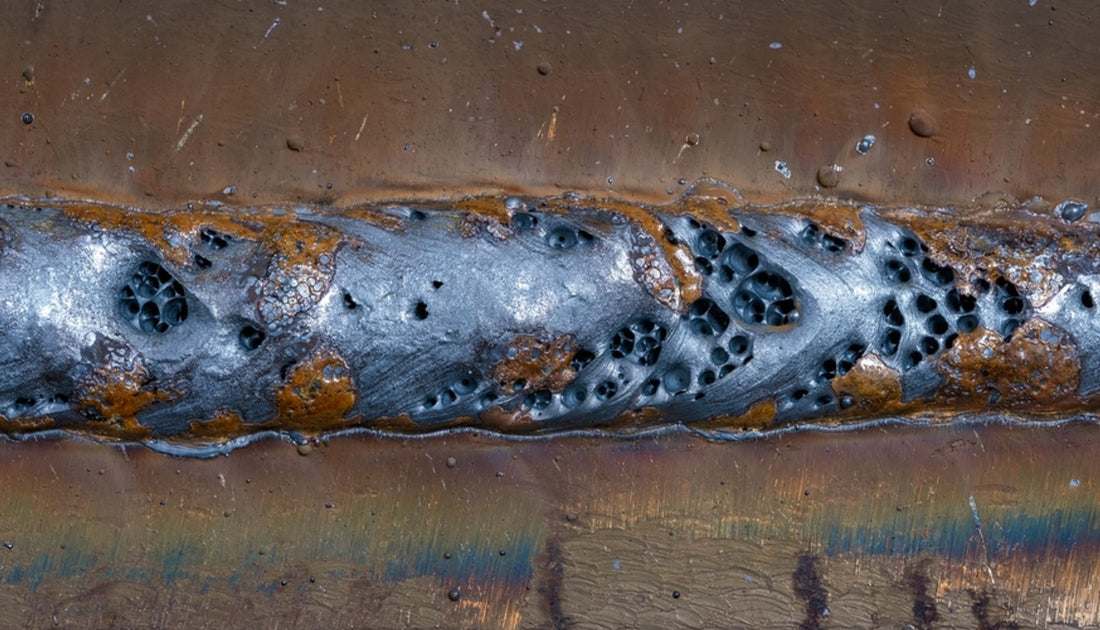
Prevention Techniques Review
Given the detrimental impact of porosity on weld quality, effective prevention strategies are crucial to maintaining the structural integrity of welded joints. Additionally, selecting the suitable welding specifications, such as voltage, present, and travel speed, can help decrease the threat of porosity formation. By integrating these avoidance techniques into welding practices, the incident of porosity can be considerably lowered, leading to stronger and a lot more trusted welded joints.
Relevance of Proper Protecting
Appropriate protecting in welding plays a crucial role in preventing climatic contamination and guaranteeing the stability of welded joints. Securing gases, such as argon, helium, or a combination of see both, are frequently utilized to protect the weld swimming pool from responding with elements airborne like oxygen and nitrogen. When these responsive elements enter into contact with the hot weld swimming pool, they can trigger porosity, causing weak welds with decreased mechanical residential properties.

Insufficient securing can result in numerous defects like porosity, spatter, and oxidation, endangering the structural honesty of the welded joint. As a result, sticking to proper securing practices is important to produce top notch welds with very little defects and make sure the longevity and dependability of the bonded parts (What is Porosity).
Surveillance and Control Approaches
Just how can welders effectively keep an eye on and manage the welding process to guarantee ideal results read more and prevent issues like porosity? By continuously monitoring these variables, welders can identify inconsistencies from the ideal problems and make instant modifications to protect against porosity development.

Additionally, applying appropriate training programs for welders is vital for monitoring and controlling the welding procedure efficiently. What is Porosity. Enlightening welders on the value of preserving regular criteria, such as correct gas protecting and travel rate, can assist prevent porosity concerns. Regular analyses and accreditations can also make certain that welders excel in surveillance and managing welding processes
Furthermore, using automated welding systems can enhance surveillance and control abilities. These systems can precisely control welding specifications, decreasing the possibility of human mistake and making certain consistent weld quality. By incorporating sophisticated monitoring innovations, training programs, and automated systems, welders can effectively keep an eye on and control the welding process to decrease porosity flaws and achieve high-quality welds.
Final Thought

Comments on “What is Porosity in Welding: Typical Resources and Efficient Solutions”